Surface Finishing Tutorial
#129 Anti-corrosion Plating
Category : Electroplating
September 7, 2012
Various products and parts are used mostly in the atmosphere.There are corrosive environments in the air, where the products are exposed to in some degrees, such as moisture, oxidizing atmosphere, sulfide atmosphere, and salts.The platings applied to the products in order to protect them from these environments are called "Anti-corrosive platings (also called Anti-rusting platings).
The most frequently used industrial material is steel and it is well known that the most suitable plating for steel is zinc plating.It is often used for ornamental products that require some degree of corrosion protection.The following are an outline of various anti-corrosive platings that can withstand harsher corrosive environments.
[Table]Anti-corrosive plating types and applications
Plating Type | Characteristics and Applications |
Zinc PlatingPlating bath types- Cyanide Bath- Zincate Bath- Acidic Bath | Due to the anti-corrosive property of zinc (Zinc is well known as a sacrificial anode of steel. This is because zinc's single electrode potential is less noble in comparison to iron, and the zinc dissolving before the iron prevents iron from dissolving.) and the anti-corrosive nature of the chromate process over the zinc plating, this is often used as anti-corrosive plating for steel.This is a zinc plating bath customarily has been in usage, and is used for press formed components, bolts & nuts and etc. It has good plating thickness uniformity and post plating machinability. The cyanide bath contains highly toxic cyanide, and the alternative bath containing no cyanide has harder plate coating than the cyanide bath.Compare to the two alkaline baths listed above, this has better electric current efficiency, and and steel and cast iron can be plated. Also, it causes little hydrogen embrittlement. |
Cadmium Plating | This plating is indispensable for ships and aircrafts since it is especially resistant against salts. As with the zinc plating, chromate process is applied. |
Tin-zinc alloy plating | It has anti-corrosive performance next to the cadmium plating. It has good solderability, paint coating adhesion, and post plating machinability, and often used for electrical components. |
Zinc-Nickel Alloy Plating | This is an anti-corrosion plating of high corrosion resistance, and colored chromate processed plating shows multi-fold corrosion resistance of the zinc chromate processed products. Because it does not cause hydrogen embrittlement, it is used for automotive parts and etc. made of steel and steel alloys. |
Zinc-Iron Alloy Plating | High corrosion resistance as listed above. Colored chromate processed plating has 5 micro-meters of coating thickness and withstands 2000 hours or more of salt water spray test. Glossy, colored, or black chromate process can be selected. |
|
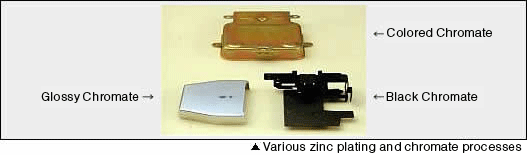