(1)What is thermal spraying?
When building heavy, thick, long, and large structures as Seto-ohashi Bridge, adopting anti-corrosion measures is particularly important.Under the painted exterior, the interface between the based paint film and the steel substrate is treated with "metallic spraying" using metals such as zinc.This treatment improves the anti-corrosion properties and reduces the maintenance cost.
In Japan, metallic spraying is called "metallikon". This is one of the surface treatment methods to form metal films on the surfaces of steel products by melting metal wires made of zinc or copper using frame's heat and spraying with compressed air. The products treated with this processing can withstand severe corrosion conditions.In addition to enhancing the corrosion resistance, thermal spraying to metal surfaces using ceramics is also common when it is necessary to improve the abrasion and heat resistance.
In recent years, these surface treatment technologies are widely adopted not only in the industrial equipment for increasing resistance to corrosion, rust, abrasion and heat, as well as for the build up, it is also adopted in dental implants and artificial bones in order to improve biocompatibility.
JIS defines thermal spraying as follows:
A method of forming a film by melting spraying materials using combustion or electric energy and spraying the molten or semi-molten particles onto a substrate |
|
(2)Classification of thermal spraying methods
Thermal spraying methods can be classified by the heat source used for melting spraying materials, types of spraying materials, purposes of the application, and so on.Thermal spraying can be classified by the spraying heat source as shown in [Table 1].Thermal spraying can be classified by the spraying materials as shown in [Table 2].
[Table 1] Classification of thermal spraying methods by heat source
Oxygen fuel spraying | Frame spraying | Wire flame spraying Rod frame spraying Powder frame spraying |
Detonation frame spraying | |
Electric spraying | Arc spraying Plasma spraying Wire explosion spraying |
|
[Table 2] Classification of thermal spraying methods by spraying materials
Zinc spraying | Zn |
Aluminum spraying | AL |
Zinc-aluminum alloy spraying | Zn-AL |
Self-fluxing alloy spraying | Ni-B-Si, Ni-Cr-B-Si, Co-Ni-Cr-B-Si, and so on |
Ceramic spraying | AL2O3, AL2O3-TiO2, TiO2, ZrO2, ZrO2-Y2O3, and so on |
Cermet spraying | Oxides, carbides, nitrides, borides, silicides, and medals |
Plastic spraying | Nylon, epoxy, etc. |
|
Thermal spraying is also classified by the following purposes of application: spraying for prevention of corrosion, rust and abrasion, heat-resistant spraying, thermal barrier spraying, build up spraying, spray forming, and so on.
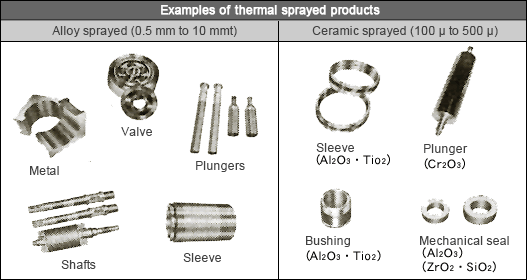